Lift Breakdowns – Our top 5 recommendations for prevention
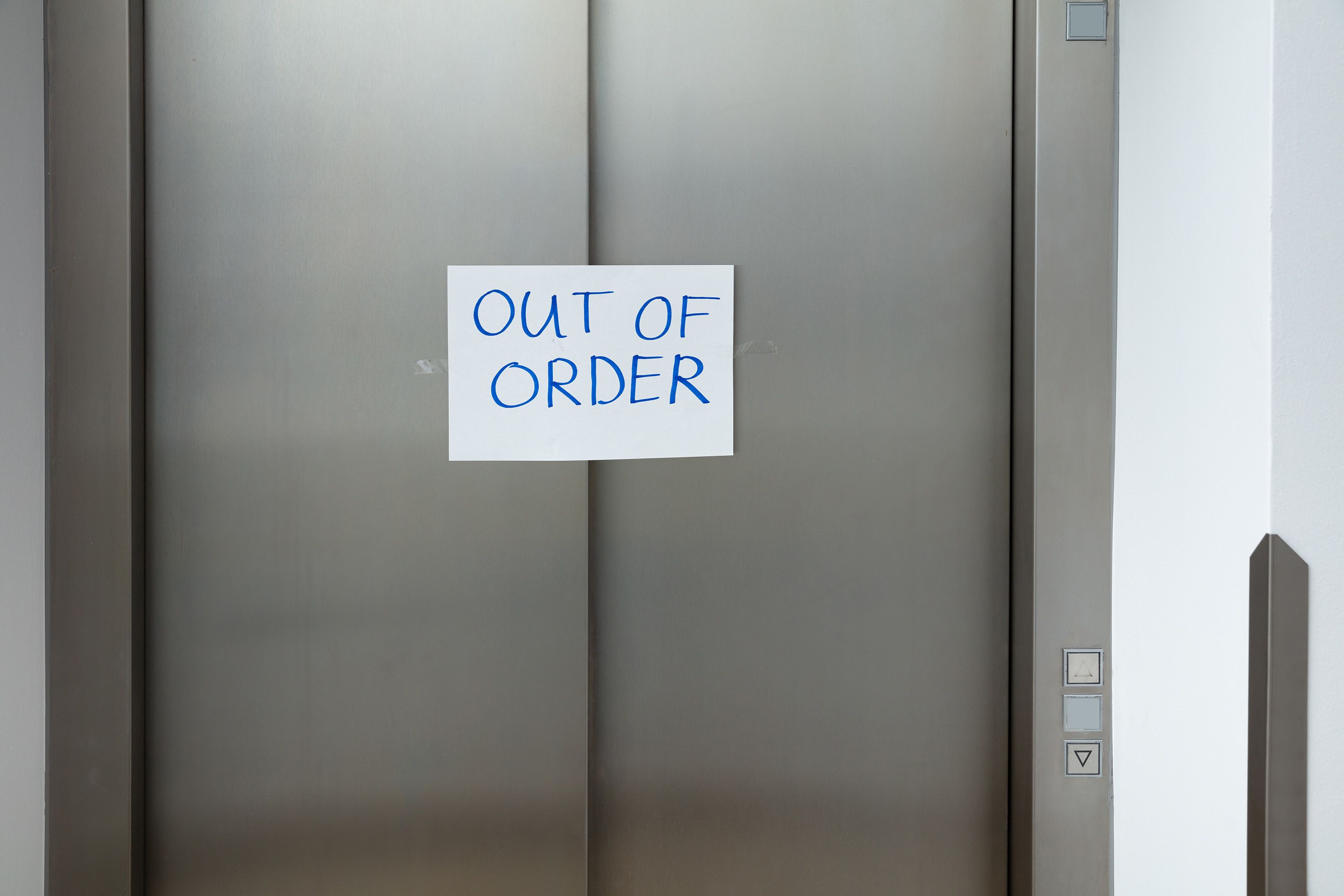
Lift breakdowns are troublesome for both building owners and the users of the lift. They are an important means of transporting passengers and goods, and are fundamental to maintaining efficient traffic flows inside some of the largest and most complex buildings.
When a lift breaks down, building operations can grind to a halt. Every building suffers considerable disruption when a lift fails, regardless of whether it's a hospital, hotel, shopping centre, office block, apartment building or airport, for example.
Here are our top five recommendations for building owners, and those responsible for the lifts within their properties, to prevent unnecessary breakdowns and failures:
1. Stringent maintenance programme
To implement a stringent maintenance programme, you will need to have a competent specialist regularly check your equipment. This check-up will need to be in line with the manufacturer's recommended schedule. Lift Consultants appointed by the building owners will often draw up a maintenance contract. The contract will cover the correct maintenance for the lift(s) depending on age, use and environment.
A regular inspection routine delivered by a competent specialist should give you the assurance of both the relevant technical expertise and the rapid supply of spare parts. These regimes must be specific and tailored to the age, traffic flow, location and vulnerability of the lift. If correctly delivered, a proactive maintenance regime will:
- improve the life of the lift
- extend the time between call backs
- maximise reliability
- reduce the risk of accidents and litigation
2. Statutory inspections
Lifts carrying passengers require inspection by a ‘competent person’, with a maximum interval of six months between inspections. Goods-only lifts must be examined at least every 12 months. This is an important legislative requirement that should be undertaken in accordance with the Lifting Operations & Lifting Equipment Regulations 1998 (LOLER). Unfortunately, it may not always be possible for your lifts to be examined on the planned date if the lift is out of service, or unavailable at the time which is why we offer emergency LOLER inspections to get your lifts back in service quickly.
To avoid conflicts of interest, ideally an independent third party would carry out these inspections rather than the maintenance contractor.
3. Daily on-site functional tests
There are functional tests you can undertake on a daily basis to check the current state of your lifts:
Emergency Communications System
A working emergency communication system is a must at all times. Automatic remote checking every 72 hours is a statutory requirement for all new lift installations. However, for existing lifts, first check whether this facility is available. If not, put a process in place that tests the system at least every three days.
Lighting
Regularly check the lighting and promptly replace any bulbs as and when required.
Lift thresholds
Check the levelling of the lift, as the lift threshold should be level with each floor it opens onto. Any significant variation will create a serious trip hazard.
Door tracks
Door tracks need to be kept clear. The most common cause of breakdowns is the doors failing to open or close. A building’s cleaning routine should include vacuuming out and regular cleaning of the tracks.
Door safety devices
Carry out regular checks on door safety devices. These features prevent injury by reversing the doors if an obstruction is detected.
Strange noises
Listen for noises when the lift is travelling up and down. Early detection that something looks and sounds wrong can prevent a lift failure. Report any noises to your maintenance provider.
Car push buttons
Check all the landing and car push buttons work and the lift travels to the correct floor.
4. Correct use of your lifts
A lift's use is restricted by its design, so using a lift correctly is one of the most important ways to maintain your lift. It will be more susceptible to damage and breakdown if it's being used for alternative reasons. Is it a passenger lift but being used for goods? Is the lift being overloaded? Are there too many passengers using the lift at any given time?
5. Educate your users
Educating users of lifts is really important, as this can reduce the number of lift breakdowns that occur. Lift users should never interfere with lift equipment, and that includes simple things like putting a hand between two closing doors.
Hitting the car doors, or forcing them open, can cause electronic components to miss-align, which is the single most frequent cause of lift breakdowns. However, user education can help prevent this. You can reduce the number of lift breakdowns within your building(s) by users taking more care using lifts.
Keep debris and litter away from your lifts. When debris gathers in the lift pit, it will take additional time and therefore cost for the maintenance specialist to clear.
Lift Breakdowns Overview
- The most common cause of lift breakdowns is from the doors failing to open or close.
- The design of the lift restricts its use; always use it correctly.
- Educating users is fundamental for maintaining your lift.
- Implement daily checks to minimise lift breakdowns.
If you would like to discuss minimising your lift breakdowns, please contact one of our specialists for a free telephone consultation: 01206 399555 or get in touch via our website